Historical Perspective and Technological Evolution:
Cold heading, a metalworking process, dates back to the 19th century when it was primarily used for manufacturing nails and screws. However, over time, advancements in materials science, metallurgy, and manufacturing technology have propelled cold heading machines into a pivotal role in modern industry. These machines are now capable of producing a wide range of fasteners and components with unprecedented precision and efficiency.
Key Applications:
Cold heading machines are utilized across various industries for the production of a multitude of components, including but not limited to:
1. Fasteners: Cold heading technology is most commonly associated with the production of screws, bolts, and other fasteners. These components are used in construction, automotive, aerospace, and countless other applications.
2. Electrical Components: Cold heading machines manufacture electrical connectors, terminals, and pins used in electronic and electrical equipment.
3. Automotive Parts: Components such as wheel bolts, engine parts, and specialized automotive fasteners are efficiently produced using cold heading technology.
4. Aerospace Hardware: Precision and quality are paramount in the aerospace industry, making cold heading machines instrumental in manufacturing aircraft components like rivets and specialized bolts.
5. Medical Devices: Precision is equally critical in the medical field, where cold heading machines are used to produce components for surgical instruments and medical equipment.
6. Consumer Electronics: The production of components for smartphones, laptops, and other consumer electronics benefits from the precision and efficiency of cold heading machines.
7. Construction Materials: Fasteners, bolts, and anchors used in construction are often manufactured using cold heading technology.
Key Advantages:
The adoption and evolution of cold heading machines offer a range of benefits to the manufacturing industry:
1. Precision: Cold heading machines can produce components with extremely tight tolerances, ensuring consistency and reliability in various applications.
2. Efficiency: Automation and high production rates enable manufacturers to produce large quantities of components in a relatively short time, reducing labor costs.
3. Material Savings: Cold heading minimizes material waste by efficiently forming components from wire or rod stock, reducing material costs.
4. Customization: Manufacturers can easily adjust cold heading machines to produce a wide range of component types and sizes, providing versatility to cater to specific customer requirements.
5. Quality Control: Advanced quality control systems are integrated into these machines, ensuring the production of high-quality, defect-free components.
6. Energy Efficiency: Modern cold heading machines are designed to be energy-efficient, contributing to reduced operating costs and environmental sustainability.
Future Prospects:
The future of cold heading technology holds promising prospects in several areas:
1. Sustainability: Continued advancements in energy efficiency and material usage will contribute to more sustainable manufacturing practices.
2. Digital Integration: Cold heading machines will increasingly integrate with digital technologies, offering real-time data analysis and predictive maintenance capabilities.
3. Automation: Automation will play a more significant role, enhancing efficiency and reducing the need for manual labor.
4. Enhanced Materials: Innovations in materials science will allow cold heading machines to work with a broader range of materials, expanding their applications.
5. Customization: The ability to quickly reconfigure cold heading machines for different component types will remain a key focus, enabling manufacturers to adapt to changing market demands.
the evolution of cold heading machines has been instrumental in reshaping the manufacturing industry. These machines offer a wide range of applications, advantages, and future prospects, from fasteners and automotive parts to medical devices and consumer electronics. As technology continues to advance, the role of cold heading in manufacturing is likely to expand further, contributing to more cost-effective, high-quality production across various sectors.
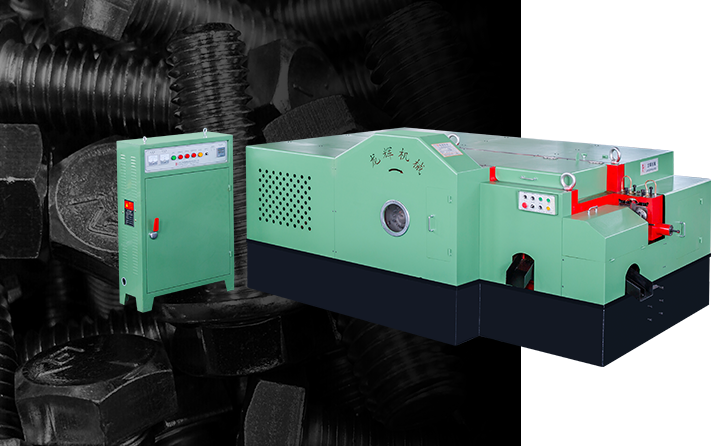